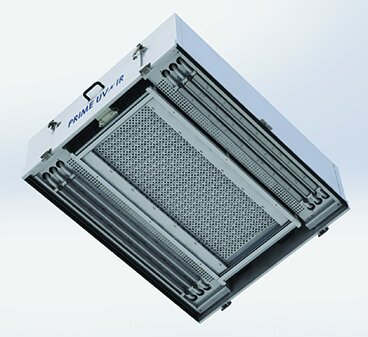
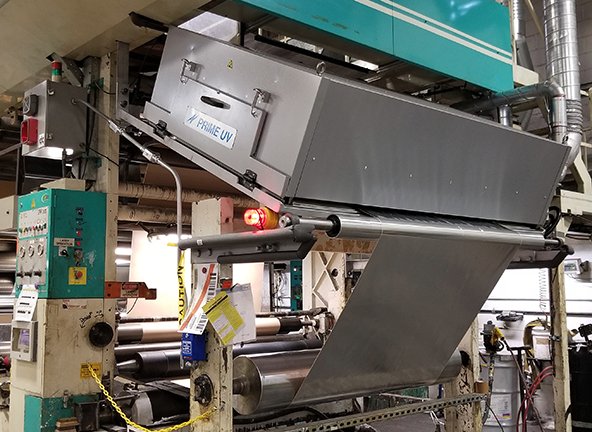
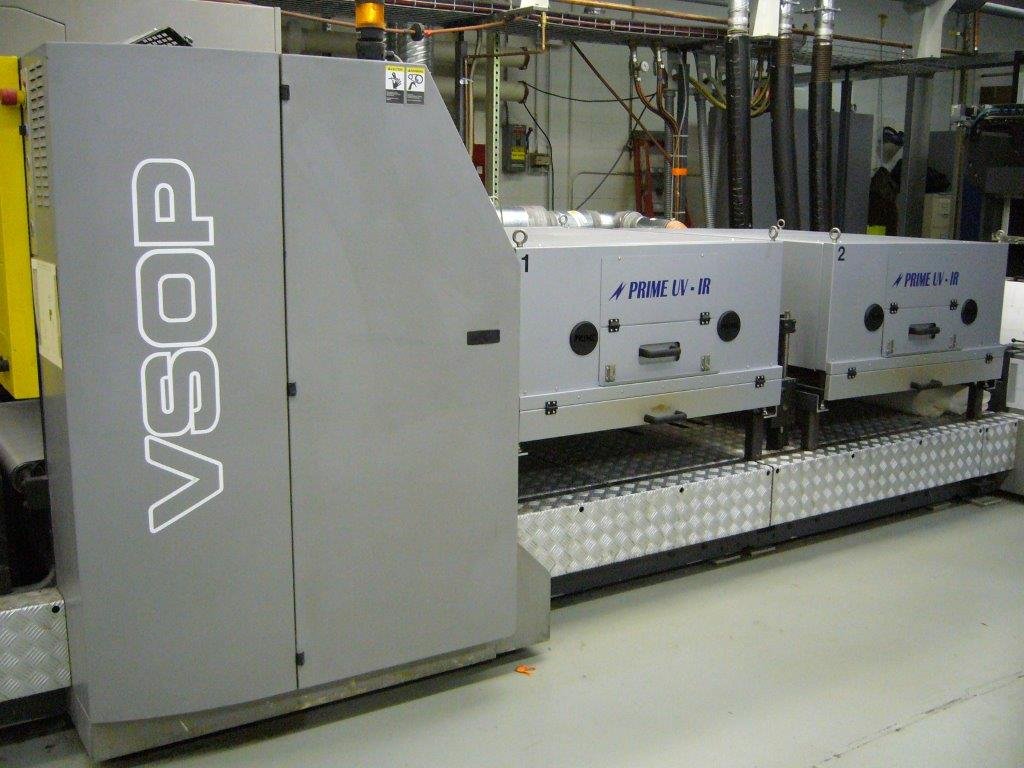
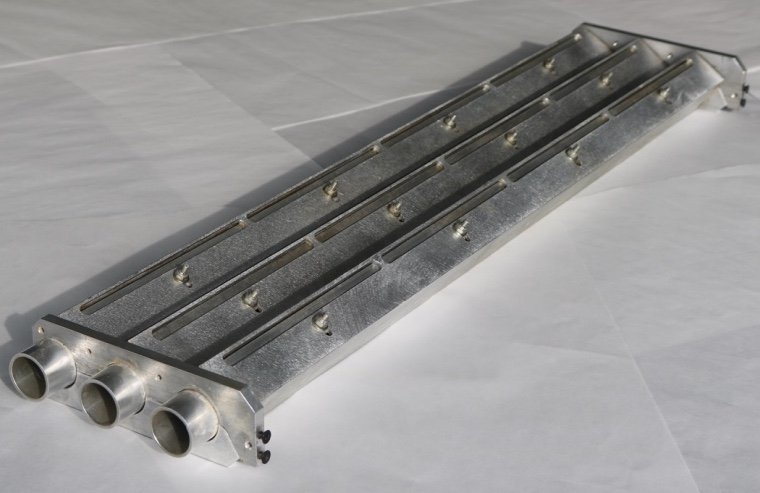
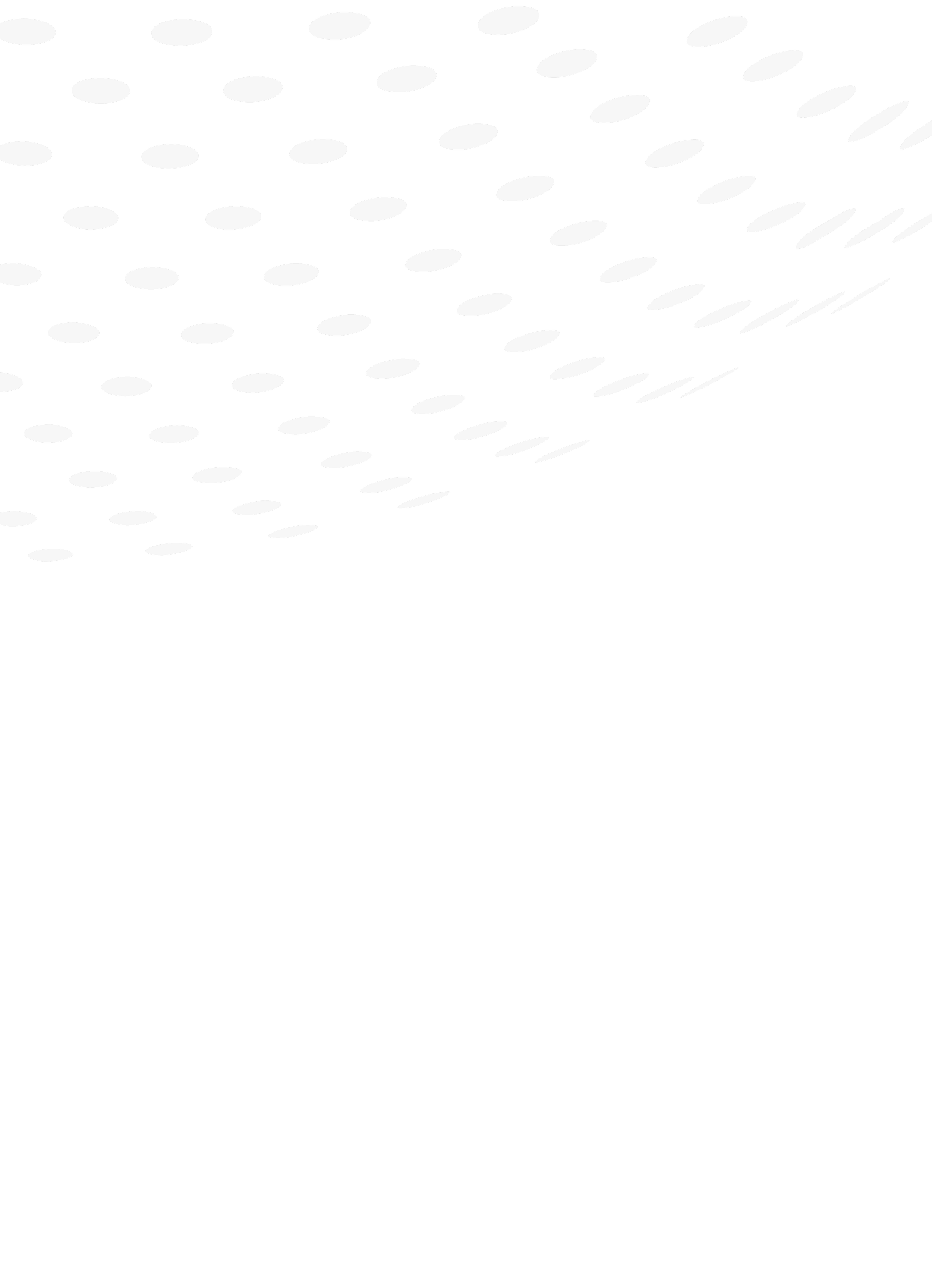
IR Flexographic Printing Business Applications
Until fairly recently, the mid to wide web flexographic printing industry relied heavily on solvent-based inks, but today the use of water-based inks is on the rise.
The main reasons for this change are to provide increased operator safety and improved environmental sustainability. In addition, the use of water-based inks dramatically reduces the costs associated with VOC control and the fact that in many areas of the world, the use of solvent-based inks has been banned or financially discouraged.
Water-based inks offer a far safer and much more eco-sustainable solution.
Today water-based inks can be formulated to contain little to no Volatile Organic Compounds (VOCSs.) Most water-based ink formulations show less than 25% the VOC emissions of the solvent-based inks. This often will eliminate the need to install and maintain expensive systems like a Regenerative Thermal Oxidizer. This very costly and space-intensive piece of equipment converts these toxic VOC emissions into harmless inert byproducts like carbon dioxide, water vapor and usable heat. However, not 100% of the VOCs are destroyed and some VOCs are still emitted into our environment.
Aside from these significant cost savings, flexographic printing with water-based inks allows printers to operate in areas of the world in which solvent-based inks are banned or discouraged, making it possible to continue or establish new flexo printing operations in these regions
Another significant benefit of water-based inks is the elimination of the fire hazard associated with solvent-based inks due to water-based ink’s low volatility. These inks are far less toxic for workers and they emit minimal odors.
Water-based inks flexographic printing challenges and how to solve them
Why do printers still use solvent-based inks?
One reason was the higher quality of the resulting printed images; however, with today’s technology water-based ink formulators have bridged the gap and provide inks that provide beautiful printed images.
Other reasons include the much faster drying time with solvent-based inks coupled with the greater energy required for the removal of water in water-based inks. These factors caused slower production process speeds when using water-based inks.
However, drying time is no longer an issue. Prime’s IR-AK6 HYBRID Dryer is designed and manufactured to deliver exceptional drying results with water-based inks. Prime’s IR-AK6 HYBRID Dryer combines the best of two drying technologies to produce a dryer superior to the rest. Add Prime’s IR-AK6 dryer to existing dryers to dramatically increase process speeds or replace other drying technology to greatly reduce energy usage and improve operating efficiencies and speed.
Designed for customization, Prime’s IR-AK6 can be easily designed to meet specific drying requirements and/or applications. Add Prime’s IR-AK6 Hybrid dryer to improve print performance while increasing production speeds.
Recommended prime products for this application
Get in Touch with a Product and Application Specialist
Contact us to learn how Prime UV-IR’s curing and drying solutions can improve your production process, reduce your energy consumption and expand your product offerings.