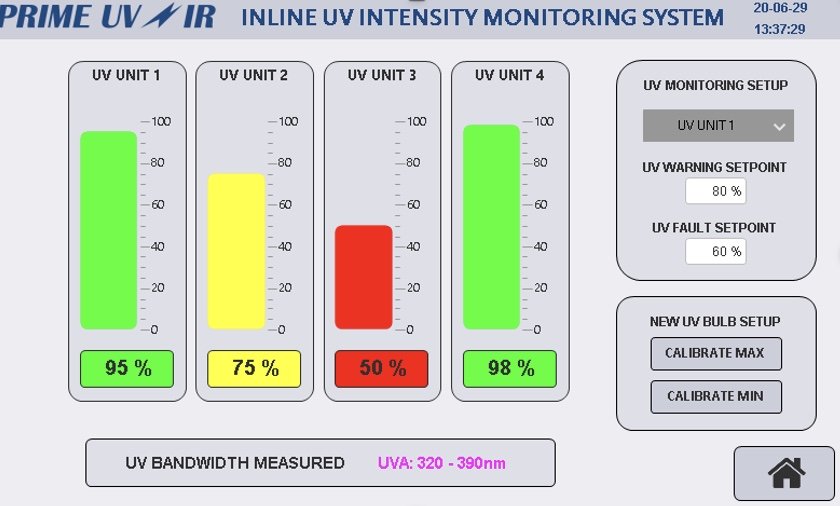
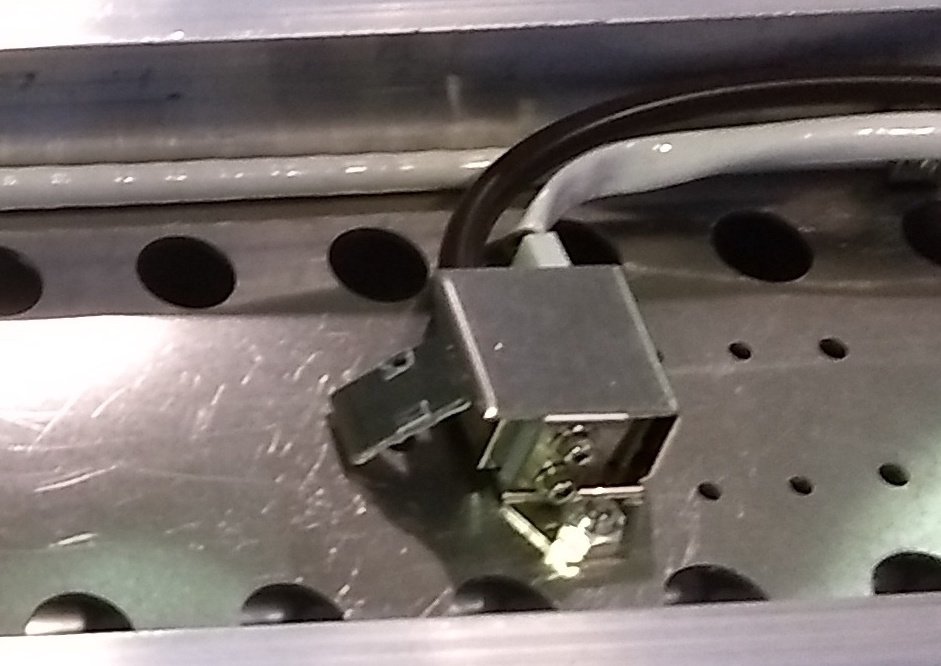
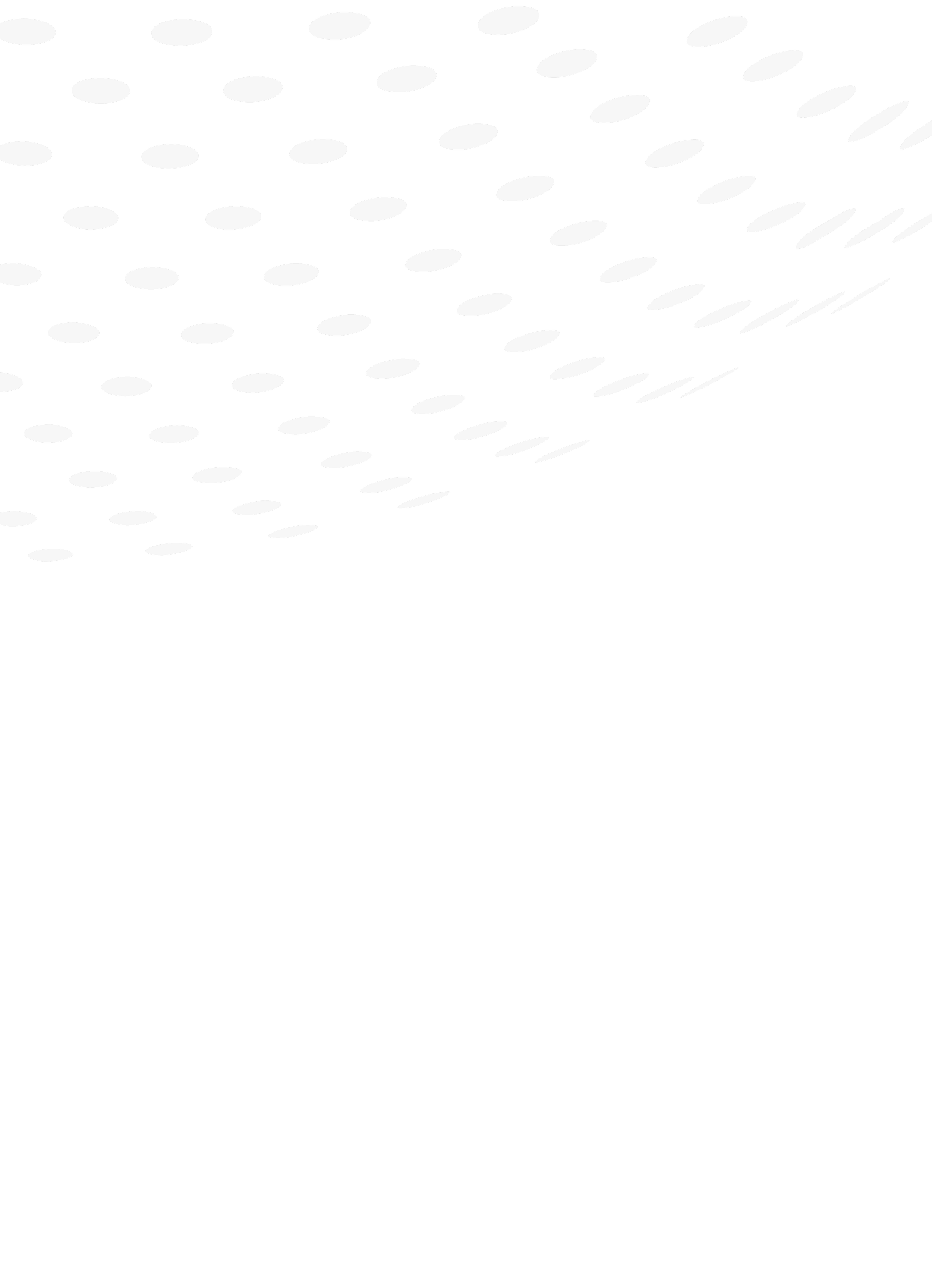
UV MEASUREMENT & PROCESS CONTROL
Integrating Prime UV Intensity Monitors into the UV system enables companies to measure UV energy emitted and then define, track and control the UV printing and UV coating process.
Many security printers, packaging and converting companies print and coat critical products worth thousands of dollars. Other companies print and coat substrates used in food packaging. Both types of companies should employ a means to ensure the product being UV printed or UV coated is properly cured. One very effective way to do this is to measure the UV energy output to ensure that the UV energy being emitted and delivered to the substrate is within a clearly defined UV curing process window.
There are 2 types of UV energy measurement devices: Relative & Absolute.
Relative Instruments: relative units, electronic signal proportional to lamp brightness (% intensity), in-line continuous monitoring, feedback to UV system PLC.
Absolute Instruments: absolute units (measure actual mJ and mW/cm2 UV energy emitted) at each UV processing unit.
Both vary in price. However, a company may utilize either option to establish and properly define a safe UV curing process window.
The amount of UV energy emitted is measured in 2 ways: UV Intensity (Peak UV Irradiance) and UV Dosage (Total Radiant Energy Density.)
UV Intensity (Peak UV Irradiance)
Expressed in Watts or milliWatts per square centimeter (W/cm2 or mW/cm2.)
Critical to ensure proper depth of cure, penetration through pigments and opaque colors, process speed, cure rate.
Adhesion to the substrate
UVV wavelengths have better penetration than UVC.
Irradiance required not always expressed.
Intensity and Irradiance often used interchangeably in UV curing applications-irradiance proper term.
Significance of UV Irradiance:
All inks, coatings, or adhesives will absorb the UV arriving at the surface, but the radiant power available deeper within the ink/coating film will depend on the absorption in the ink/coating film. The higher the radiant power at the surface, the higher the power at any depth within the material.
The reduction of light energy as it passes into or through any material is described by the Beer- Lambert law. Energy, which is not absorbed in an upper layer of the film and not reflected, is transmitted and available to lower layers, according to the following expression:
Iαλ = Iολ (1-10-Αλ) d
Ιο is the incident energy at wavelength λ, Ια is the energy absorbed, Αλ is absorbance at wavelength λ, and d is the depth form the surface or film thickness.
Peak Irradiance is the highest power level of radiant energy at the work surface.
UV Dosage (Radiant UV Energy Density)
Expressed in Joules or milliJoules per square centimeter (J/cm2 or mJ/cm2)
Incorporates time as part of the measurement
One Watt for One Second = One Joule
Area under the irradiance curve.
Often the only UV exposure guide number supplied.
Important for total and complete cure of material.
Inversely proportional to line speed
Ex= Ey ∙ Vy/Vx Ey= 400 mJ/cm2 Vy= 40 fpm
If Vx moves to 80 fpm, Ex= ?
DOSE-RESPONSIVE VS PEAK RESPONSIVE MATERIALS
“Dose” is the most-often reported measure of UV exposure, but when referenced alone, without other information, it is an incomplete specification. Dose is included here as an important factor in process specification because it is the only one which includes time. In many cases, the only controllable variable in a curing process is speed (or time). In such instances, dose is the only variable, which can be changed.
Please be aware that clear coatings and varnishes tend to be dose- responsive. In other words, increasing dose alone may increase their practical cure speed. Practically, increasing the number of exposures under second or successive lamps will increase cure speed proportionally. However, this is becoming an exception rather than the rule.
However, higher Irradiance provides both greater depth of UV energy penetration into UV chemistry and higher UV cure efficiency. This may also result in better UV chemistry adhesion to the substrate.
To establish and clearly define a safe UV Cure Process Window a company must first define the acceptable and safe range:
The range in which the UV curing process will provide the desired results & characteristics which may include any of the following:
Adhesion, hardness, flexibility, gloss, texture, stain or scratch resistance, chemical rub, cross hatch, abrasion rub, color ID, registration.
Align several windows (may be more than one process window.)
Ideal if the Process Window is forgiving and has a wide latitude.
To establish and define Process Windows, first:
Create
Reproduce & transfer the process to production.
Optimize the cured properties of end product.
Quantify optical conditions for desired result. These may include the following:
Effective UV irradiance
Spectral Distribution
Exposure profile/time (UV Dose)
Infrared (Heat)
Monitoring
Verify that the key optical conditions remain within specified limits. Daily, Weekly, etc. – dependent upon application.
Measure and document changes in equipment.
Establishing a Process or Cure Window
It takes work and time-invest now, invest when things are working!
Operator Training, ISO/Procedure Documentation.
Define your lower limits and document the readings.
Increase line speed until undercure occurs. Record readings and cushion by 20%.
Monitor your readings by job, hour, shift or day as required to ensure quality and that you are operating within your Process Window(s.)
Some benefits of including Prime UV measurement devices in-line on your production line include:
Continuous Monitoring of each UV unit’s bulb intensity.
Set up critical safety thresholds to help ensure your product meets customer’s performance criteria.
Use captured information to establish proper preventive maintenance schedule for servicing of Prime UV Curing system.
Determine when to clean and to replace UV bulbs and UV reflectors.
Maximize UV Process speeds while minimizing energy consumption.
Collect critical data for statistical process and quality control.
GMP “Good Manufacturing Practices” – use this data to obtain GMP Certification.
Recommended prime products for this TECHNOLOGY
Get in Touch with a Product and Application Specialist
Contact us to learn how Prime UV-IR’s curing and drying solutions can improve your production process, reduce your energy consumption and expand your product offerings.